Okay, so I’ve been messing around with this titanium chronograph project for a while now, and I figured I’d share my process. It’s been a real trip, let me tell you.
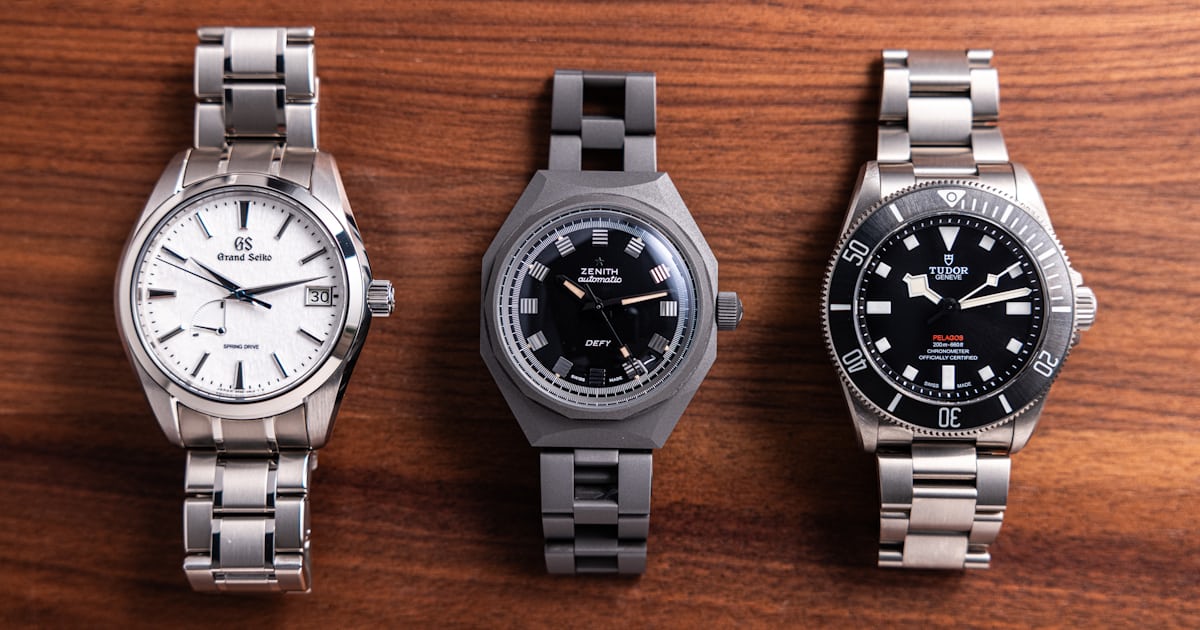
First off, I got it into my head that I wanted to make something with titanium. I mean, why not? It’s got that cool factor, right? Grade 5 titanium, or Ti6Al4V as the pros call it, seemed like the way to go. I did a little digging and found out it’s the most common type of titanium alloy. It’s tough, it’s light, and get this—the price isn’t insane compared to some other fancy metals.
But man, getting my hands on this stuff and actually turning it into a watch? That’s a whole different story. Turns out, working with titanium is not easy, and it gets expensive fast. I mean, they don’t just hand this stuff out at the local hardware store. You need some serious gear and know-how to refine it and shape it into anything useful, let alone a watch.
I started by trying to find the material. Not easy, let me tell you. And then I had to learn how to actually work with it. I thought about going with Grade 4 titanium, which is apparently the strongest pure form, but it is way harder to shape into anything, it is not very moldable. Grade 5 is better in that way. I was in my garage, trying to bend and shape this titanium, and let’s just say it was not pretty. Lots of trial and error. I even tried to read up on some tips, but it’s not the same as actually doing it yourself, you know?
The process of making it
- Sourcing the Titanium: First step, I had to get my hands on some Grade 5 titanium. I spent hours online, calling up suppliers, and even visiting a few metal workshops. Finally found a place that would sell me a small batch without me having to sell a kidney.
- Designing the Watch: Next, I sketched out what I wanted this watch to look like. I’m no artist, but I managed to draw something that resembled a watch. I wanted it to be sleek and modern, but also kind of classic, you know?
- Cutting and Shaping: This was the hardest part. Cutting titanium is no joke. I had to buy some special tools, and even then, it was tough. Shaping it was even harder. I tried bending it, hammering it, even heating it up. Let’s just say I ruined a few pieces before I got the hang of it.
- Assembling the Parts: Once I had all the pieces cut and shaped, I had to put them together. This involved a lot of tiny screws and a magnifying glass. My fingers felt like sausages, and I dropped those tiny screws more times than I can count.
- Adding the Movement: I decided to buy a ready-made watch movement because, let’s face it, I’m not that good. I found a decent one online, and fitting it into the titanium case was another challenge. It barely fit, but I managed to squeeze it in there.
- Finishing Touches: Finally, I polished the titanium to give it that nice, shiny look. I also added a leather strap that I thought looked pretty good with the titanium case.
After a lot of sweat, and maybe a few tears, I finally had something that looked like a watch. And let me tell you, holding it in my hand, it felt pretty awesome. It’s not perfect, but it’s mine, and I made it from scratch. It’s heavy, it’s a bit rough around the edges, but it works. And it’s made of titanium, which is just cool. The whole thing took way longer than I thought it would, but hey, I learned a lot. And I’ve got a one-of-a-kind watch to show for it. Would I do it again? Probably not. But it was definitely an experience.